Step-by-Step Guide to Operational Excellence: Where to Start?
The pursuit of operational excellence is essential for maintenance and service companies that want to increase efficiency, reduce waste and ensure quality. This article presents a practical guide with fundamental methodologies to start this process.
PROFESSIONALS
3/8/202511 min read
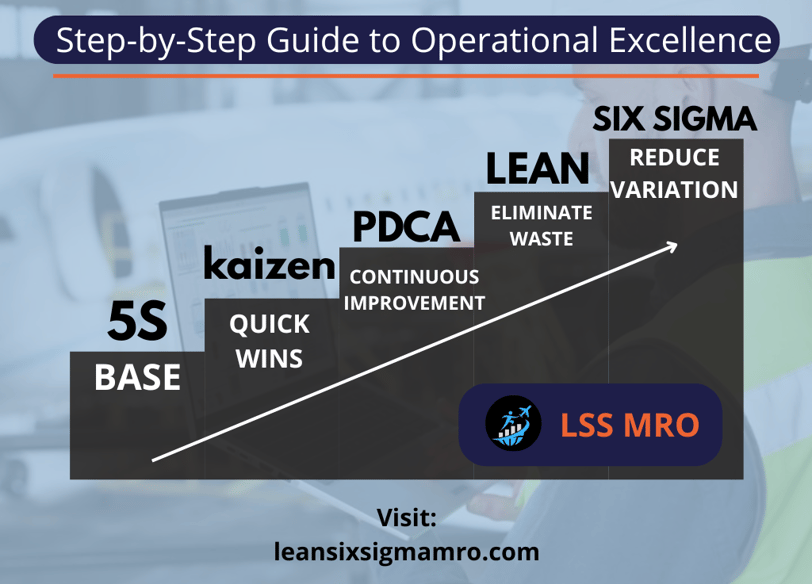
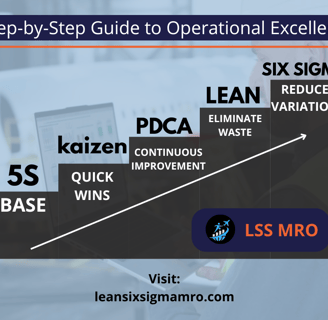
Step-by-Step Guide to Operational Excellence: Where to Start?
1. 5S – Organization as the Basis of Efficiency
If you are starting your journey towards operational excellence, the first fundamental step is to structure your work environment efficiently. Before optimizing processes, reducing costs or implementing advanced technologies, it is necessary to establish order and discipline. To do this, we use the 5S methodology, which is one of the pillars of Lean and one of the first steps towards continuous improvement.
What is 5S?
5S is a Japanese methodology created to promote organization, cleanliness and efficiency in the workplace. Its name comes from five Japanese words, which represent the five essential principles for transforming any productive environment:
Seiri (Sense of Use)
Seiton (Sense of Organization)
Seiso (Sense of Cleanliness)
Seiketsu (Sense of Standardization)
Shitsuke (Sense of Discipline)
This methodology doesn’t just apply to factories or workshops. It can be used in any environment, from offices to hospitals and service companies. If you want to start your journey towards continuous improvement, applying 5S to your daily routine is a great place to start.
Why is 5S the first step to operational excellence?
Imagine trying to improve a process in an environment where tools are scattered, unnecessary materials are piled up, and standards are lacking. Without organization, any attempt at optimization will be ineffective.
5S is the foundation because it creates a waste-free environment where people can work more efficiently, safely, and productively. When applied well, 5S reduces time wasted searching for tools, improves workplace safety, and increases the quality of operations.
Now, let's explore each of the five senses and understand how to apply them.
The 5 Senses of 5S and How to Apply Them
1. Seiri (Sense of Use) – What is really necessary?
Objective: Remove from the environment everything that is not essential for work.
🔹 What does this mean in practice?
Separate useful items from unnecessary ones.
Eliminate tools, documents or materials that are not used.
Reduce the accumulation of items that only take up space and hinder the workflow.
📌 Exemple: In a maintenance workshop, rarely used tools take up space on the bench, making it difficult to access the most frequently used ones. Applying Seiri means identifying which tools are essential and storing or discarding those that are not needed.
2. Seiton (Sense of Organization) – Each thing in its place
Objective: Create an organized system so everyone knows where to find and store each item.
🔹 What does this mean in practice?
Define specific locations for each tool or document.
Use labels, signs and visual patterns.
Ensure that everything is within reach with minimum effort.
📌 Exemple: In the aviation industry, every part and tool needs to be in the right place to avoid delays and errors. In the maintenance hangar, implementing an organized layout and clear labeling significantly reduces the time wasted searching for items.
3. Seiso (Sense of Cleanliness) – Cleaning as preventive maintenance
Objetive: Keep the environment clean at all times to avoid failures, increase efficiency and ensure safety.
🔹 What does this mean in practice?
Create the habit of cleaning the work environment daily.
Identify and eliminate sources of dirt and contamination.
Develop a sense of collective responsibility for cleanliness.
📌 Exemple:On an overhead line, dirt build-up on tools or components can lead to serious failures. Applying Seiso means ensuring that equipment is always clean and ready for use, preventing future problems.
4. Seiketsu (Sense of Standardization) – Creating clear rules
Objetivo: Establish visual and operational standards to keep the first three senses functioning continuously.
🔹 What does this mean in practice?
Create checklists and routines to maintain organization and cleanliness.
Define clear rules for maintaining order.
Use colors, labels, and visual markings to make it easier to identify materials and processes.
📌 Exemple: In an aeronautical parts warehouse, standardization in the arrangement of items and adequate signage prevents errors in removing the wrong parts, ensuring greater efficiency in the operation.
5. Shitsuke (Sense of Discipline) – Making 5S a Habit
Objective: Create an environment where the practice of 5S becomes a habit, and not just an isolated action.
🔹 What does this mean in practice?
Encourage staff to follow 5S practices every day.
Conduct audits and training to reinforce the culture.
Make 5S part of the organizational culture.
📌 Exemple: In a maintenance company, if 5S is just an isolated event, disorganization will quickly return. Applying Shitsuke means creating regular training, engaging the team and reinforcing discipline so that improvement is constant.
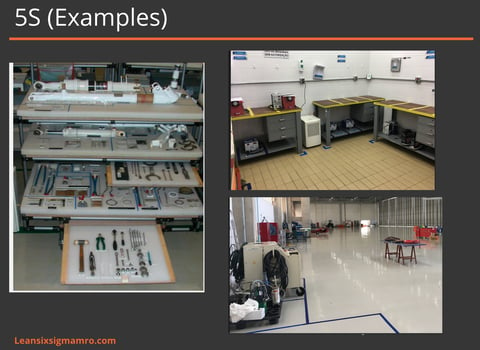
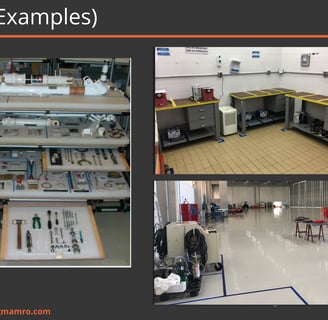
2. Kaizen – The Philosophy of Continuous Improvement
If you have already applied 5S and structured an organized and efficient work environment, the next step in your journey toward operational excellence is ensuring that improvements never stop. This is the role of Kaizen, a fundamental philosophy for keeping processes in constant evolution.
What is Kaizen?
Kaizen is a Japanese word that means "change for the better." In the business and industrial context, Kaizen represents a continuous improvement process, where small daily changes accumulate into significant results over time.
The concept was developed in Japan after World War II and became one of the key pillars of Lean Manufacturing. However, Kaizen is not limited to factories—it can be applied in any sector, including maintenance, service provision, and aviation.
🔹 Kaizen is not a one-time event but an ongoing process!
Why is Kaizen Essential for Operational Excellence?
Imagine a company that only improves its processes when a major problem arises. This creates instability and waste. Kaizen takes the opposite approach: small improvements made every day lead to significant long-term results.
By applying Kaizen, your team will always seek ways to reduce waste, improve efficiency, and prevent recurring errors. This fosters a culture of innovation and continuous learning.
📌 Example: In an aircraft maintenance hangar, a technician notices that the arrangement of tools on the workbench causes him to waste time searching for items. Instead of just accepting this, he suggests reorganizing the space. This small adjustment can save valuable minutes on each task, resulting in hours saved over a month.
The Principles of Kaizen
To understand Kaizen, it’s essential to know its fundamental principles:
1. Elimination of Waste (Muda)
🔹 Objective: Identify and reduce any activity that does not add value to the customer.
📌 Example: In aviation, time wasted waiting for parts or reworking tasks due to errors are forms of waste that Kaizen aims to eliminate.
2. Small Steps, Big Results
🔹 Objective: Instead of pursuing major overhauls, Kaizen focuses on small, continuous improvements.
📌 Example: If a company reduces the time needed for maintenance by just 1%, this small gain translates into massive improvements over a year.
3. Involvement of Everyone
🔹 Objective: Anyone can suggest improvements, from technicians to top management.
📌 Example: A maintenance inspector notices that a checklist could be reorganized for easier reading. Small suggestions like this create efficiency for the entire team.
4. Standardization After Improvement
🔹 Objective: When a process is improved, it must be documented and standardized to ensure that everyone adopts the new practice.
📌 Example: If a maintenance team discovers a faster and safer way to replace a component, this new method should be recorded so that everyone follows the same standard.
5. Culture of Continuous Improvement
🔹 Objective: Kaizen should not be a temporary project but an ingrained company culture.
📌 Example: An airline encourages employees to suggest improvements every month. These suggestions are reviewed, and when approved, they are implemented to enhance operational efficiency.
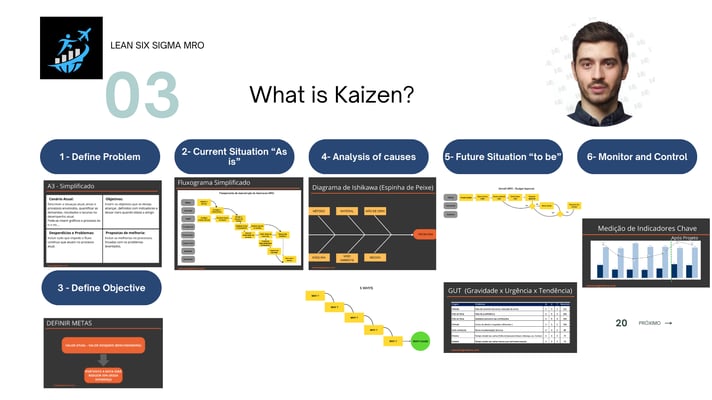
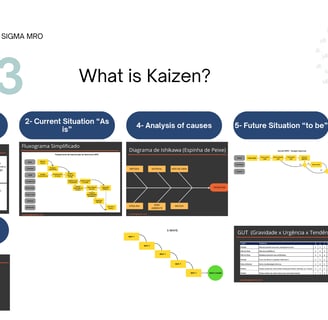
How to Apply Kaizen in Practice?
Step 1: Identify a Problem or Improvement Opportunity
Start by observing the process and identifying where waste, failures, or delays occur.
💡 Helpful Questions:
✔ What are the most frequent issues in operations?
✔ Are there tasks that require excessive time or effort?
✔ Are there recurring errors that could be avoided?
Step 2: Involve the Team in the Solution
Kaizen should be collaborative. Gather those involved in the process and ask for improvement suggestions.
📌 Example: In a maintenance department, technicians can meet to discuss ways to reduce waiting times for parts.
Step 3: Implement Small Changes Immediately
Don’t wait months to implement an improvement. Small adjustments can be made quickly.
📌 Example: If a team notices that a tool could be more accessible, this change can be made immediately.
Step 4: Evaluate the Results
After implementation, measure the impact of the improvement. If the results are positive, standardize the new practice.
📌 Example: If a new tool layout saves time, that organization should become the standard for the entire team.
Step 5: Repeat the Process Continuously
The Kaizen cycle never ends. There are always new opportunities for improvement.
📌 Example: After optimizing tool placement, the team can focus on reducing component replacement times, and so on.
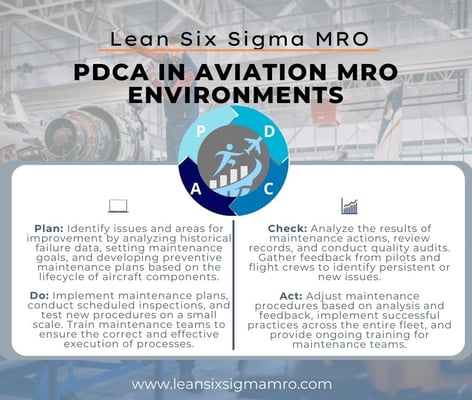
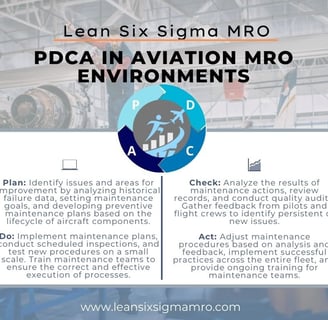
3. PDCA – The Foundation of Management for Continuous Improvement
If you want to start your journey toward operational excellence, you need a methodology that allows you to identify problems, test solutions, and continuously improve processes. The PDCA Cycle (Plan-Do-Check-Act) is this essential framework to ensure constant and sustainable improvements.
Used across various industries, from aircraft maintenance to service management, PDCA provides a simple and effective path to solve problems and increase process efficiency.
What is PDCA?
PDCA is a continuous four-step cycle designed to promote process improvement and problem-solving. It can be applied to any area and is fundamental to maintaining a high standard of quality.
The 4 Steps of the PDCA Cycle:
1️⃣ Plan– Identify the problem and define an action plan.
2️⃣ Do – Implement the planned solution.
3️⃣ Check – Evaluate the results and verify if there was improvement.
4️⃣ Act – Standardize what worked or correct what needs adjustment.
This cycle never ends! With each new improvement, it starts over, ensuring that processes are always evolving.
4. Lean – Waste Elimination and Focus on Value
If you want to achieve operational excellence, you need to learn to see what adds value and what generates waste in processes. Lean is a methodology focused precisely on this: increasing efficiency by eliminating waste and ensuring that every activity contributes to delivering value to the customer.
In the Maintenance, Repair, and Operations (MRO) sector, Lean can be a significant competitive advantage, helping companies reduce costs, improve timelines, and increase service reliability.
What is Lean?
Lean is a management philosophy based on the Toyota Production System (TPS), which seeks to optimize processes by eliminating waste. It applies to any sector, from manufacturing to services and aircraft maintenance.
In Lean, the golden rule is simple:
✔ Value → Everything the customer is willing to pay for.
❌ Waste → Everything that consumes resources without generating value.
This means that when applying Lean, you learn to focus on what is essential and eliminate what does not add results.
The 8 Wastes of Lean Applied to Services and MRO
Lean classifies waste into eight main types. Here’s how they affect services and maintenance:
1️⃣ Overproduction – Doing more than necessary before it’s needed. Example: Excessive preventive maintenance without real need.
2️⃣ Waiting – Time wasted waiting for parts, approvals, or information.
3️⃣ Transportation – Unnecessary movement of parts and equipment.
4️⃣ Overprocessing – Activities that do not add value, such as unnecessary bureaucracy.
5️⃣ Excess Inventory – Keeping large quantities of parts idle without need.
6️⃣ Unnecessary Motion – Unnecessary movement of technicians, leading to wasted time.
7️⃣ Defects and Rework – Errors that require correction, such as poorly executed maintenance.
8️⃣ Underutilized Talent – Failing to leverage employees’ potential to improve processes.
📌 Example: An airline notices constant delays in maintenance because the necessary parts are not always available. By applying Lean, the company adopts a reliability-based forecasting system, ensuring the right parts are in the right place before they are needed.
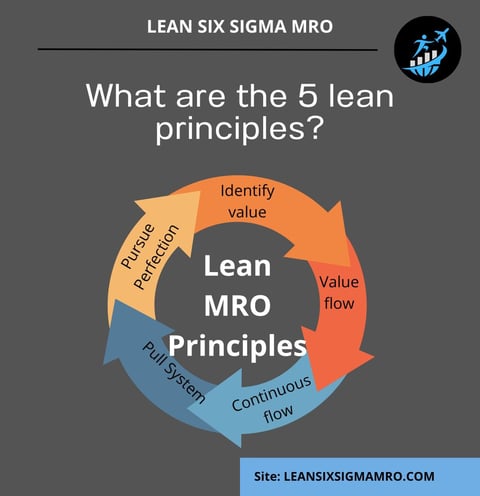
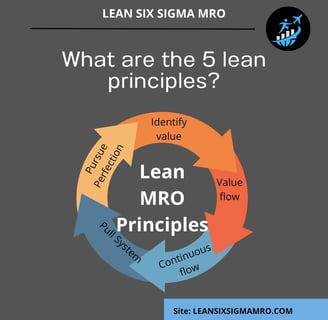
With our Courses we promise to open the doors to a new era of possibilities. Advance to the next level with our Aviation Lean Course.
Are you ready to take a leap in your career in the Aviation industry?
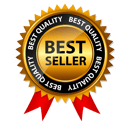

Only in Portuguese
Soon in English
How to Apply Lean in Practice?
To adopt Lean, follow these essential steps:
🔹 Step 1: Identify Value for the Customer
Ask yourself: what really matters to the customer? This could be shorter maintenance time, lower costs, or higher reliability.
✔ Example: An airline wants to reduce maintenance time without compromising safety.
🔹 Step 2: Map the Value Stream
Analyze the entire path a service or product takes, from request to delivery. Identify where the waste is.
✔ Example: In the aircraft maintenance process, a value stream map can show which steps cause delays and which can be optimized.
🔹 Step 3: Create a Continuous Flow
Organize processes so that activities flow without interruptions, eliminating waiting times and bottlenecks.
✔ Example: Adjust the logistics of parts so they are always available at the right time, without excess inventory.
🔹 Step 4: Implement a Pull System
Instead of producing or performing activities based on uncertain forecasts, a pull system only activates processes when there is real demand.
✔ Example: In aircraft maintenance, systems like Just in Time can be used to ensure the right parts are requested at the right and necessary time, avoiding waste.
🔹 Step 5: Pursue Continuous Improvement
Lean never ends! With each optimization, it’s necessary to review processes and seek new opportunities for improvement.
✔ Example: After reducing maintenance time, the company analyzes data and discovers it can improve even further with new tools or techniques.
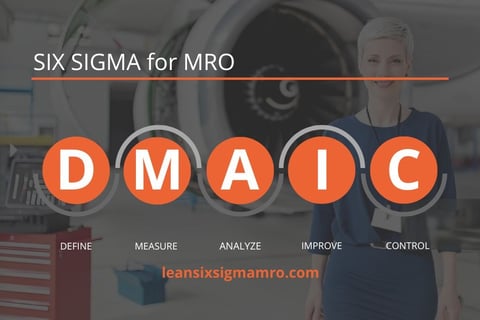
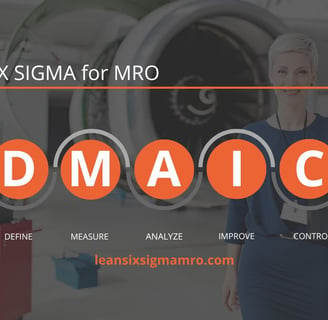
What is Six Sigma?
Six Sigma is a data- and statistics-based process improvement approach designed to reduce variability and eliminate defects. It was developed by Motorola in the 1980s and gained global popularity for its ability to improve quality and efficiency.
The core idea of Six Sigma is to minimize errors as much as possible, aiming for a quality level where only 3.4 defects occur per 1 million opportunities.
In the context of maintenance and services, this means ensuring predictable and reliable processes, reducing errors that could lead to delays, rework, or critical failures.
Why is Variability a Problem?
Variability in processes leads to:
❌ Delays – If a process does not follow a stable standard, it may take longer than expected.
❌ Rework – Errors and failures require corrections, wasting time and resources.
❌ Quality Issues – Inconsistency can compromise safety and service reliability.
❌ High Costs – The more variation, the more waste, and the higher the expenses.
📌 Example: An airline notices that the time required for aircraft inspection varies significantly from one day to the next. This impacts flight scheduling and causes delays. By applying Six Sigma, the company identifies the causes of this variation (such as lack of parts or differences in process execution) and implements improvements to standardize and stabilize inspection time.
How Does Six Sigma Work?
Six Sigma uses a structured method to solve problems and improve processes, called DMAIC.
🔹 Step 1: Define
The first step is to identify the problem and clearly define the improvement goal.
✔ Example: Reduce variation in aircraft maintenance time.
🔹 Step 2: Measure
In this phase, we collect data to understand the current performance of the process and identify the real extent of the problem.
✔ Example: Measure maintenance times over several weeks to identify patterns and inconsistencies.
🔹 Step 3: Analyze
With the collected data, we investigate the root causes of variation and defects.
✔ Example: The analysis may reveal that a lack of parts in stock is one of the factors causing delays.
🔹 Step 4: Improve
Here, solutions are implemented to reduce variability and optimize the process.
✔ Example: Create a replenishment system based on predictability to ensure parts are available before maintenance begins.
🔹 Step 5: Control
After implementing improvements, it is essential to ensure they are maintained over time.
✔ Example: Continuously monitor maintenance times and create a dashboard of indicators to prevent problems from recurring.
Conclusion – The Path to Operational Excellence
The pursuit of operational excellence does not happen overnight. It requires discipline, knowledge, and the structured application of proven methodologies such as 5S, Kaizen, PDCA, Lean, and Six Sigma. Each of these steps complements the other, and together, they form the foundation for more efficient, reliable, and competitive processes.
If you want to stand out in the maintenance market or any service sector, continuous improvement must be part of your professional routine. The knowledge and application of these tools not only increase your company's efficiency but also enhance your value as a professional.
📌 And now, what’s the next step?
🚀 Continue your learning journey and accelerate your career!At Lean Six Sigma MRO, you’ll find specialized courses that will help you apply these methodologies in a practical and strategic way.