Lean Methodology focuses on Maintenance Service
Did you know that Lean methodology isn’t just for manufacturing? It’s a game-changer in MRO services too! We explore how Lean principles tackle the unique challenges of intangible services like maintenance, repair, and overhaul. From eliminating waste to focusing on customer value and driving continuous improvement, discover how Lean transforms service processes. Learn the five key Lean principles and how they optimize workflows, reduce delays, and ensure exceptional outcomes in MRO
CONCEPTS
12/29/20242 min read
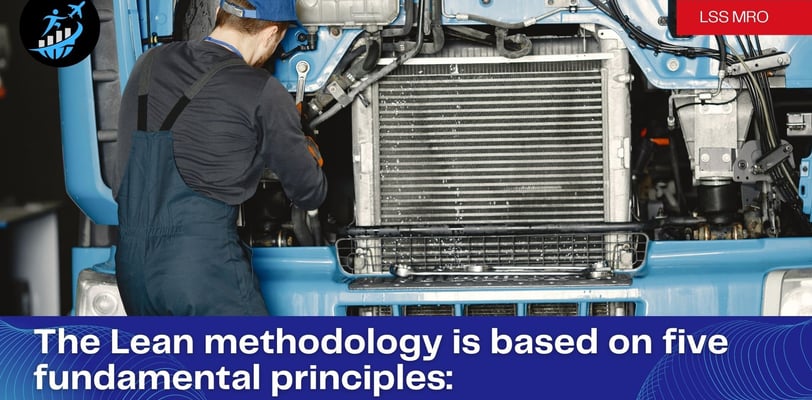
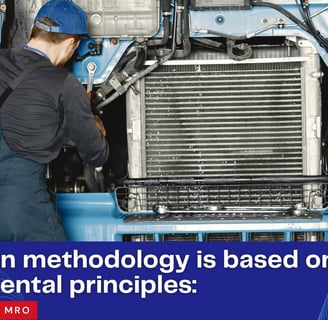
How Lean Methodology Transforms MRO Services
In the dynamic world of Maintenance, Repair, and Overhaul (MRO), achieving efficiency and delivering value to customers are constant challenges. Unlike manufacturing, MRO services deal with intangible and variable tasks, making it crucial to establish well-defined processes. This is where Lean methodology steps in as a powerful framework to overcome complexities and optimize operations.
The Challenges in MRO Services
Services like MRO are inherently intangible—you can't see or touch the outcomes until the process is complete. This intangibility often leads to inconsistencies, inefficiencies, and difficulty in measuring performance. Additionally, MRO operations involve diverse tasks, from inspecting components to ensuring compliance with safety regulations. Without clearly defined processes, these tasks can become chaotic, resulting in delays, waste, and dissatisfied customers.
By adopting Lean methodology, MRO organizations can standardize their workflows, establish measurable outcomes, and create a system that ensures consistency and reliability.
The Benefits of Lean in MRO
Eliminating Waste: Lean focuses on identifying and removing non-value-added activities. In MRO, this could mean minimizing unnecessary movement of parts, reducing waiting times for tools or documentation, and ensuring that only required maintenance is performed.
Customer Value: Lean emphasizes delivering value from the customer’s perspective. For MRO, this means focusing on quick turnarounds, ensuring safety and quality, and providing transparency in the service process.
Continuous Improvement: Lean fosters a culture of ongoing enhancement. MRO teams are encouraged to evaluate their processes regularly, identify bottlenecks, and implement improvements to ensure sustainable efficiency.
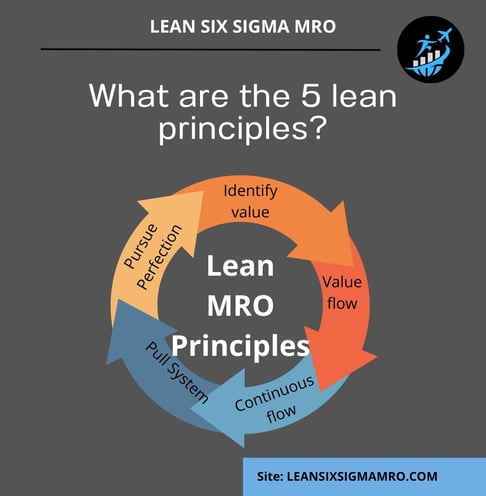
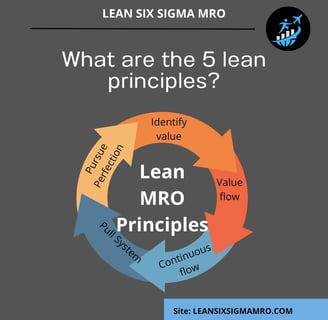
The Five Lean Principles
Value Definition: Understand what the customer values most—for MRO, this could be reliability, speed, or cost-effectiveness.
Value Stream Mapping: Visualize the entire process, from the receipt of an aircraft or component to its delivery, identifying areas of waste and opportunities for improvement.
Flow Creation: Ensure smooth and uninterrupted workflow by addressing delays, optimizing resources, and maintaining a balanced workload.
Pull System: Implement a pull-based system where work is initiated based on demand, avoiding overproduction and excess inventory.
Perfection: Strive for excellence by continuously refining processes and aiming for zero defects or delays.
Conclusion
Lean methodology offers a structured approach to tackle the unique challenges of MRO services. By defining processes, eliminating waste, and focusing on continuous improvement, organizations can not only meet but exceed customer expectations. Lean isn’t just a methodology; it’s a mindset that drives efficiency and value.
Ready to transform your MRO operations with Lean principles?